Case Study: SAP Business One Implementation at Bangalore Metallurgical Private Limited
Company Overview
Bangalore Metallurgical Private Limited
India
Metal Processing & Foundry
60
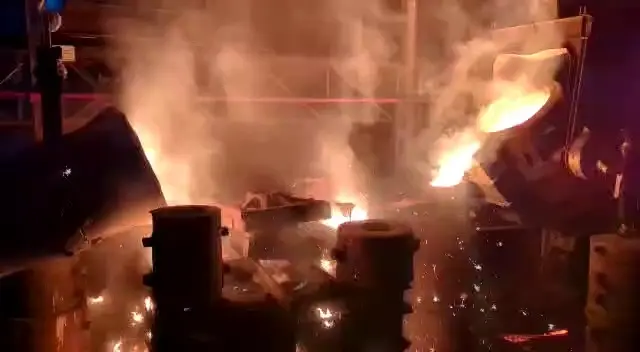
Bangalore Metallurgical Private Limited is a leading manufacturer and supplier of high-quality metal components, catering to industries such as automotive, aerospace, and heavy engineering. Specialising in precision casting, machining, and metal treatment, the company plays a vital role in the metal processing and foundry sector.
With increasing customer demands and production complexities, Bangalore Metallurgical sought a comprehensive ERP solution to optimise production workflows, enhance quality control, and manage subcontracting operations more effectively.
Challenges Faced
Lack of Production Visibility & Routing Challenges
- Manual tracking of production processes led to delays and inefficiencies.
- Absence of a structured routing system resulted in inconsistent workflow execution.
Inefficient Quality Inspection Process
- Raw material quality was not systematically monitored, leading to higher defect rates.
- Lack of real-time quality control measures caused delays in manufacturing.
Subcontracting & Vendor Management Issues
- Tracking outsourced work orders and vendor performance was difficult.
- Material movement between company and subcontractors lacked transparency and efficiency.
Limited Financial & Inventory Control
- Disjointed financial reporting and stock management led to inaccurate costing.
- Manual procurement and inventory processes caused material shortages and overstocking.
Scalability & Future Readiness Concerns
- The existing system lacked scalability for increasing production demand.
- The company required a solution that could support long-term growth and automation.
SAP Business One Implementation: The Solution
Production Planning & Routing
Integrated a structured production routing system for real-time tracking of workflow stages.
Incoming Quality Inspection (IQI)
Automated quality checks to ensure raw materials met production standards before processing.
Subcontracting Management
Streamlined tracking of outsourced work orders, material flow, and vendor coordination.
Financial Management
Enhanced accounting, taxation (GST compliance), and financial reporting for improved cost tracking.
Inventory & Material Management
Implemented real-time stock tracking and procurement planning for seamless production.
Sales & Purchase Management
Standardised vendor order processing, invoicing, and contract tracking for better supply chain efficiency.
Key Benefits & Business Impact
Optimised Production Planning & Workflow
- Real-time visibility into production routing, minimizing delays.
- Improved resource allocation and capacity planning.
Enhanced Quality Control & Compliance
- Automated incoming quality inspections, reducing defective raw materials and rework costs.
- Improved product consistency and adherence to industry standards.
Efficient Subcontracting & Vendor Management
- Enhanced tracking of outsourced work, reducing inefficiencies in material movement and supplier coordination.
- Reduced vendor delays and improved vendor collaboration.
Improved Financial & Inventory Control
- Automated financial reporting with faster GST compliance and taxation management.
- Accurate stock management, preventing overstocking and material shortages.
Scalability for Future Growth
- ERP-driven automation allowing the company to scale operations efficiently.